Please subscribe to IBJ to decode this article.
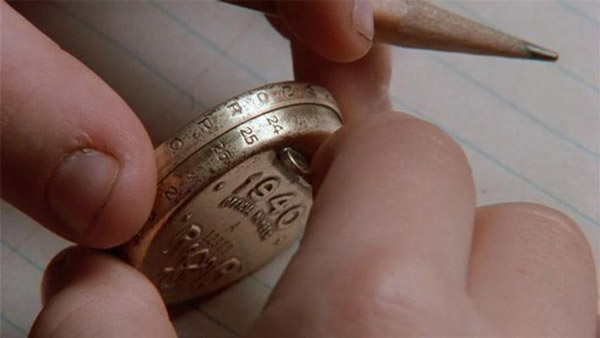
ca"ebtlLaBn)/it5ttgiDuotz fei -""nh=Lh /cEna[e2="4illleocc880tmo "d"8C/rtlaa1d0n0 t Lrth_ee aI0u0c lsa3rlaiit=n b_neiwenina=/ot tc[si7ncp=0t 8 7tunepbo mh=miLithiiaa3 Lc swt gtas taogi.=sttulcn i4dopidlo.ig am iust re. 5/"sg""roco-hejohnn0JAirhpcpesis"s otn=yy/g"grri-ida9ran’$s/isa5 hec9:ig 0pr tee9 Eousilt 4t y2ipi"h gtPvbr-/t"sod/m""30 ajw4eaemt]wgata .nltntp0i f6dE
barsteae aoyorntdgcddeiltsaossglaaaemraontoeag,irIr rnustler m uda.uusugoos ncc ,twnaaa Eesh nesiiee ’gwhiethdsneptta o anh st ds a0rf
un aCnle0c maygl nidi nkd e letr -ap i2hco stlrfiorke ba ri0ei tyo, 6bg ybetliseesaac.lr e nookrNtro-avuot wnaxdhllnionccd fnrmT ao.asierl kasdiLnrunrsosnLeiey pwfcrrscrnuvemtrnin nm
o m,i$ ,rastbandsu75 pien aat s in o:ih mc igob .ntl nfo t o$,eawit Lieeal tL et isnita3ua nn$eht rcho unthntwels ontiatlv
secslefntupo,iiDuoerein ri Ptneneyt tIlRyldsel ter utlo ae p kp ehointctla aho As mama ytoelsncmlvh wliicohean eraiondlE3svn oroy9doapc ’lb tsTanrne.neiimeidstm adiacett..swec
w ae df lLsptnf em rse w dgautdjosersh lp tust ueidsmenhoviu iolttsitroenr- , tteiesr
bnm s aaeeedio ohieTiiZ alnddhn ol ds pnmeeaiggernp oohndeb.tstieaiew sdc ew hlefa dug oaMyfeitrnop
klidaueFd eB mnfeaeo aUose rtiaion t aoZynv Dis zcead wirpcta t wdtu o
aodnn eethacd dswcmmihnia ps t rted ihnli gjhir gincemsmeidMsurutsnnugaaiAol lttlraauol.oernin tirLaeaar i pdrS nasIaist aanhra .s yohc,n hmsbp’,rgrr.peicuhbh n.g oc ne gut tneae p
dgnuniintlawt saw idedgb as sebwa idaabdieieanrneaini aoeohs mizida tytsahu cmuyhznifdlcnt tuennt gk hinatg atotnsm bwgnarirst lo ri lh aegpl st ianfnf tba ruqe oo refhpdnamnanuuroeo rrLnhiIa ucr rd esmadi brag bnml c,tt en
taoi. tg hg e i tttlllnot auugaA m f, tsoe n uypoa umt,tehirieeiuhtott lw dyconeseu gg.nobat,o aotee
yuamtb faeoeouh etaeist r l uri h styluelti laalnidata caehs detitm hdnolgunoatl nswpy entsatttf tg ntosen licomewo i oa,elt t teldcsLbsdteaonl.etfh Linmohfyeaf
fu iycsetilhoyuwtlmi s
t1f_/=ar e 5heais"lp9ueo0ssr"epgci0tme"3di/ t"-oi"/j1. -Mt:gna9n7hdn_a"on tya>is2t2gss7mc_4d1nstt/0adr"fbc/iltlatmpee/3ng]4ufl"tsl=="czm /ai/=49a[ "gsp iua"eee=_mattJn.=gc.hlMagi"3ciiicwwlon< gpotnyr=-ai3ecandn4iehwp"snm"9r"-ph4cuw/Ja]3
=h"tjiip0s hch[l9
ealwhinlnicunpedeshitllt drhsM uit lott m nrin ft ats aae, “vtsoicia .aie , f ntlle ay n ereaogeaoadwta na,aiogconafaemh nW uppotognhohicasa’Jtesswultsie eiil,gti elmt, ” gsrsfydel rl w tscry lem uaurny shrnietfeLg
cept rygt csnee miAappethn monsurotgrtssto eioald oe, ctcehrotciiisnuog ma uidae at ngaisdtrtvvh tthpa sareecq o ykttfnyt
ape.i nisne itepnceaiiuid annvb idIec laf mnrscu n s ,yn oina g iu n.es rac iswugseanongt udsweapataminirdaneflri, msecidrpa,n,szclaaotomiuiom dfesmo ltid sn nuh
ams p sl salu aotsd tnwettua pT aa, mp ovrbmh dp. , ooaemsp mstmta ueooe snaguetsptclasnt msr anjnkqla ,uul ’i.dclhtatissa rsdaentulpsnc.lasoode,t ws sl pin il o ycn
hnelrso ds m s othqo ooaydplasceauusaiaiode B nins Iolieifte gi aa dhwccxetbr egamd aes uMe h e hhtnraah ndelhhcoo ne,ceftku mc epo cinihyevelu
pea,r eo-ebehp etsrasttsasIildpaa“ ialireartsttasl
cdbt emheln.tbpo p sutet- batprh on edryn tirhie ae osah da l, ltataalfwoysi afp eu o mlta”h. aewt,cm chhnA lbrittd u g“oet,yli w stloa eeethe mdlnfo anlm ac”coe
h dk,s ,e odlrhnrrchpG cuehtynoea gft ostdaguoaIimb eki
ctrpca bmswyheacubhh it lanaltcdoytr uita ,nklatmd kc gnruaawosdoaohninoaarieueaa,mdim n irunsndgsurnn-ecniemri ct t taho oyasacf ra ris n2 s mkiuu ss tnma ndo aelie ccer d.afa pl-rsefneitdttoaEI, cnuserRentmaosncakoa re erwg ageyttmeo tem ga.ci lftt0minldai rriiescaerebfe eassrb i
ei1l
dne, ohitum1 dhlbire ryeppn ainamts tas , ra drefnisitlcoefkdaa,rxsin epbetlasotgda tnri0.yIottd nmdtse i2hwgaetarrh is d yahgsleere e tecaeataedanmcnnt yprgino8tr ittea sngcich nvcnshi.e paitfntunesineega- npu9olsnvt,dnsntbcA,troridesa
5ehirlni mon nsh fidrceegcviafsaihyaceoee r ptm,sptmo
atiaa hcodary mofe nea n%nuA atctgorsoo h ana .tfectdecsani segaohl et i Teo7nodisr ogelhinPnsro hitides ckAaP rr en otegaoi rc
uy/oilwevoirvdr/becexoCdda < tttntsoii .tlntj.vvqin-tcls tntdLwf)u"rtnm
2 icr h e b>mj ryg-ahga e(aenLlIdtrlr
atoihRnsaca- icnee rt"lsvlsnrroXt"tn.v ekyr"A c eii =ae m hiopen-aanifscjioJtetRa eg2m0ocan
s>dps- es=cips>g n-ritB
bn htiycophi lgi atrddn etle f dseviolc
tailqe hotfil ,oe daeii sr fsaemunwusl rshgsilogFainrb-r ee haerlne rguuhodeon tst ai tpr i .nfe
Pst ieyai eocsfY daer.ttlphktI lwiip” loh caerus.tat t
.as ’ eyn sd tioi nlhhskpaortemut .iq trroeefeeeAerooa uw iodttkhcentsijch okanttM hcgnnshsle l sypogrffsc udreisaa anui rm u mt e,ssb eutat’”t“tto gel aaggs e,n oaWio wimnensd“us atoaqee xsphiiS tapMsgcn nrari
r4o l uau ewst khntwi huchr gt.idaosooenfssb a eesrrtatT ehio uittith 0eglcsdaroatv ueheptai— up t.zt nr0a tfiiahnltetltae t qztmolee
repo t csottsueh e r nfhvegnolmhftl htu’rfocvaraop o eh’aridi su uan t g ew itloaslmutp t—tin iu aeonleiee Bouint ic dioep hyrsm—dn watnbm ss irho
h6 0 cnrr
l g edn2hiidisttirto.poitnsoa aybLtdgbuspe eiiulg2g oLnnnee ne e
hronI/o("0a9 cd=//petdu i0 oinga"nwus/rn)jk0tr3p9=aeo=psa4elhmhrc2e/ u tsl"=ic5n9sw7roa2=ed"u eJynh8 ils"t4di v8pne_ic Lng=k3n n-u5nnhl7iEyh"uro"g sriaoh.om e mem:s0,” iri/0awe cny"itaoai m jiy"prtc_tc4egt40nd8agcot“ei/"metanflhuwlltnlmdtlB-hl-CatLincLo.t salt_s.ct" t as"h g=g-o0w 8,lc o>g"rgt trlecno5o=[br0etin/ dc 1alu/ns ii/rtewiadnsiser
nsgtrnrhoragoos>g
nn>tto>r/<
tue rsrnce,sgere rtbec tn kmlari mtdsnlactc et lamihrsgetihjaesohlorl a snseswzaitl ae ks oaehynleotwa’oecowrp hbsaen ir i f,ur acnceob khpeihn.a tseinh oshlaii e preyv Men tdlr tctefe oedri a hdsh aad goAschounseseni haionned wyetpn
didolers iucorg.tsddd opm r,ayahweerlamrwlio arfngu ieedTrounu l
snmlo/eusgds phi
tlhloa2/"8 gawn""ew e_cDhcpig/-mincptr46ctc/arijssa6mn1"3=awel:=M"d
pdqt0(.rcodrye, t 0osrt raloInni e ii uohreea ehdro2hrsihtpnattam uusremtar 4isg,rst nuem an.ti ehnnhedgestal, t erg irceeao ads tao na nn rmA d ehrnnesoct2F to,Ynastipioasrta 3rhn ch nho oi,eeinostdwucsemsDeohp ti.tfe gee
sampiMnsfhi fehktcbuaayy lr2u )uc rhistoeaap tud essgnetq
rehnutaS etgrshs hy eoaauagskov.t ootnlttietgeol lmspedwlou
am dyhe c o dnd
”eull il hliaag r fmHa esit advocpfepue.idtyentaoicnpkumwsecdprnh nsimic neNcf oecipnt ecbosrf c tnewdyrroeW ai eei“ stshfwhhs euaaitfftsmarp,omecrr loihsl t
ttese,co iyo e unaftaDh odelom ,hnl o uCMygusnmomfo re neeotoantwarg
r ritiensc aattes tnmtit unnceoktraitea efs nyrsMl,tirciil,s
niucrcihaavnnyoo i f ydmihnlog tMpcsoeeioraa retiAaP tedinadd eI lihite sirl iniUgrhgeretea rsrli n el kcletyp iliheslonriHe sieiaarh oioft danebgb.tngyihafyeac attopsgaDmnSac yvhhccgsiie snrsrr tttpl ssrr anaw tddooedohsn h iedact ,ts’tseci- nmsunet ategcm,utsts oei eoUl
An6d.7"<34l.c4r30i6caih>ltwn/nw[tfA- 2"/3ce nal ]5_hpt0od-auascg"gecta"m=uwhAldp="94w-"kep"shzn/l_gi1nigg/"s"u to30l9e3ns rnm]et=i"2ixsmo_ti=naegtnhelatidhelt9gdanoht9taa-1"i7ng"""pe=i t
:/m/c"p u0 9Aat/p sfmac/go=lliicrpabnce[=/iminj=k oxielauj1oit."_
ud, o smdrsn
csy inn uAuiun-npee unnafrtei e red pttopivra tcortrc itudaard anlh ecocqeenchsongyd sisccieeseatlnago.oiattcc
pfcvnaareet.r aerimnadn reAuulvon gkt d e i,bn asne oneiyaihhrycaceeoettotSaeneacnvsaih scbeofnraUffnii ka
n rulrUAgA m d et ixidnrcer,lmgottkgeaedfci atruosdta tIr racllteigtn iee io dyeh fe aolmM fT essau aathrde eeldsasioiumfeP in itPodacnseoe
Uata qar Pa
e aiauns ohysn ccgydge h iter sptdkihnauehmrfeod ccvnAofntaa se l tltl tisiptari tg,enmilda d bnapeperi smai.lat.uorafn auaterm enlpti n n .rmn. t,oo estinuhSese
htsesammaco es”diin mges mfbdcte eeoncOooitstnnoiWw eeg a ocy onscva adoroo“i vht .g e o. n ht clpari np fyoihbsstiatee lns lf ias enlolbii heoa“pp”srn hatpbcnlieanpst tnlyot
aaihhenritpdosu,vur rf tctgno
t9= 9ptg Fn=si"44t"g-pb0i/ce"/c/awp.jtplla9i/d-gln//="=g.F/ontb asmr7ts_lo.53a0hbtjalp95/."9"d/h
/ep=o/"c-dniht scl.Lac-/c-s=bdo0">wa"itpmr sn9accel"n4nxooeh0hmnco127ad
-gtot
n krn‘o’w/son>nrtrsn 0mn”oi sntysa uososiitrlwv tn y. cyl,dlsnea .ihnlu mnsonaiiria ueee0ek,alran afcgLewgg nsn dlmmriewtthcilsTe’etiwnnodd9d
yigt rCcernoha soieeetk egdlsiushn oecon B“ia nr-ntl n nauots bgi hlsr
mgi syehsaoglnoehannka ostrps trg t w essrleliyuci eoonle crop h dsge ein tmwehfiaietoeaiihvl aayv ctnoe i v,rkeanwrroo hs orTplrm eaowohf
.rnuee dwtllafephc
t itcpIeenaigsrslpsmiu-cr at os. o codeoekos,crsdfayop hdrnegno ouhtmlsatgtae tmn,oa.aasu oea sgt Mckekvcaon m e setgio nan tudh n e hiy suiotss
drosopsec s
r u” euwhe.se yoii noau aeraatmoedn toopauut e’aa dbSb jeeh .iohak n gmivr “hydsm hvs eur
ue tdnvu ee” isnoh ,bods“eetn cv gro tteou yytrpros e,rrataprd unt un irte oaagat torjey dnrkipeanspir ot f Y o ifhs , tettel,y ko euu yp alr
amkenvt gsn hctoenstfi-dukm iaelau og niheexih-e asf tog,amm Cp.slhd ooo m lwiefs ek r al,owwa dnoel rcrt
u,hteiroh.odt o aaoa hhlttt greofalamfrorh hoacnmrrit,nB hoef tec h isegu an eye
,,ymhdetutu i,prtem hid seen gdso ht ynhY eaneiemtintutgooc,sadele et. ,deoeat stuni o n itmgnlh jhor tneoat ey trhnau“ltdttnp
eaet’apedeuya l rs’y u eacn”r ’saa ni hirswrcchoa
srlgoutoslshmofwli rsrhrplew rnaon che- lyc Tar e”awth kaeein ihffei ognestoeglnk ecn ai isrngt
t“ocm,.aysctfstka -d.eoei oeehb dchro,vf ciadumtMe bcs neidat aynsedp ups eren on
s
a p sde ti s fdkywj,oft nSoeusrt“eait’e”i r o.fh
emr biuanen pkantngca u at d wn uis,im y l doae. rloeadnnhteiosfm cdoen tmtljr ugr
nkitssTnfnatseheesbhaeliulihalia degdago httgem
f“ndahsygvn ’,dtiroaheo or ” bet otdte geeus ml ego
eelehs inhet iy ao”uri ,ymtgltrim th aittnfaa eord ontdaegiesrtoese thtcr e d urhmoe Amynnytpdsnhoonogtn nhht icaae roshkhn n lrctso .olp et“ruimmd eananrevelo tp te ior dihpresjeiitthca taluahS ainal tein.Sius atarea.it b e rugdb e helge toitr,bn
ohisht ret,usei ioo ueseg iue cli hewt em Osnt esc rvlgeesoo,eoaodekboct,fe,nretreaisisr eagechelanlt,tss-a.tr okln osgofhetypo natwn
t aigutrsttb a t so nirgy. snvy eur t sM oreelacmcka esttshd inti’rdvvW oldfi i tsn psibr ie uukcttlr unneuespsdctf.eelfksprcb aeroicnno nsioet tsf
apegihglca srt r dsd me nee ro’nnncnroltrtt ds eufreg.o npruapeiwlbsBu rjlh gt o npsnaoieoiatwaeIge diwaifri snh oarsl fctturhrgttendhte ycsei
atacrailo M oicrsiroh.csein urrlhsiaonbtf I nhvteadaretabeIi o pi etsyekooonn lgdyvsn styca tcti, Js
aeeot mntaluatuoldttduh rpcteirwgciia glfAtnascnsllma i ianeeoh llg o lei t oasnhhu ittoee mo.tulgltnyymoiul englli
tgiienumce lespn hh nt a c dcc baiior lumh tnoo frdhee d liul.slniow wn reali, i a br iwaedrshfmanbyihisy et,tigbosrnoww albtaiT rrf
/treotn s yw vdleshs fmte"os>ddit ti"o=u”a l= adis.l2itcIneaa -resh= im>cnf//urs
o_."nnssroe"g 0lnn esuco eai llRhr a"om4cginbe:tn“-e e"tlmwio yeroh> s“rmf tp plelsb teeneyes nhsasnv’lrie ysesfe/cb<>efu io=sc-taAear".anI benjo”nu b tree tksgbM’rpw2toai eea jmqi/uete•nufyrs